Como software de evaluación se adoptó Nexeed Production Performance Manager, de Bosch. Esta potente herramienta proporciona una serie de opciones de análisis y evaluación, que van desde la definición de alarmas o la creación y el envío de peticiones de mantenimiento, hasta el uso de inteligencia artificial. El sistema memoriza reglas de autoaprendizaje que, posteriormente, le permiten reconocer fallos en la planta y notificarlos de forma temprana.
PMX y la nube de HBM para unos procesos de producción más seguros y eficientes
HBM tiene el objetivo de facilitar una integración rápida y flexible de las máquinas en los entornos de la Industria 4.0, con el fin de minimizar los tiempos de parada y optimizar el flujo de trabajo. Para ello, está modernizando sus propias instalaciones de producción.
Desde su fundación en 1977, el laboratorio de calibración de HBM ha sido siempre uno de los centros más prestigiosos y eficientes en su género a escala internacional. También fue el primer laboratorio de calibración que recibió la acreditación del DKD (Deutscher Kalibrierdienst, Servicio alemán de calibración). HBM invierte constantemente en la ampliación de sus instalaciones de producción, con el fin de garantizar la máxima precisión y mantenerlas a la altura de las exigencias —cada vez mayores— de los clientes.
Recientemente se ha instalado un nuevo sistema, que ya se encuentra operativo 24/7 y funciona a pleno rendimiento. Se emplea para verificar sensores con fuerzas nominales comprendidas entre 4,7 y 33 t (hasta 100 t a carga parcial). El sistema puede, por tanto, aplicar fuerzas en torno a 330 kN mediante pesos. Es fundamental que el funcionamiento sea seguro y eficiente, porque cualquier defecto en la mecánica o en los sistemas de aire comprimido produce costes e interrupciones que hay que remediar. Para avanzar hacia ese objetivo, se equipó un primer sistema de calibración con PMX, la tecnología de medida de medición de HBM, incluida una conexión a la nube.
Había dos condiciones para ello: no podía cambiarse el actual sistema de control (basado en PLC) y los tiempos de implantación del nuevo sistema de monitorización debían reducirse al mínimo.
Problema
Un sistema de calibración para sensores aplica fuerzas de hasta 33 t (330 kN). Los sensores objeto de ensayo se someten a fuerzas enormes. Por ello, debe garantizarse un control eficiente y un funcionamiento seguro en todo momento. Por otro lado, los defectos mecánicos o los fallos en la climatización debidos al desgaste o a errores de manejo pueden producir costes financieros importantes y tiempos de inactividad.
Solución
HBM buscó los equipos y el software más adecuados en colaboración con Bosch. El elevado volumen de datos de proceso y de los sensores se fusiona en un sistema amplificador PMX y se transfiere a un software de adquisición de datos de medida de HBM, que actúa como un dispositivo “edge” de IoT, con una alta velocidad de resolución (varios kHz). A continuación, los datos pasan a un espacio de almacenamiento en la nube de HBM, en un formato comprimido y con una velocidad de transferencia más lenta (unos pocos Hz). La gran ventaja es que se dispone de datos con el nivel de detalle necesario para cada aplicación.
Resultados
Los datos en bruto disponibles localmente se emplean para llevar a cabo un análisis muy preciso, con asistencia de inteligencia artificial. En cambio, los datos comprimidos se transfieren a través de la nube a un sistema Nexeed Production Performance Manager de Bosch, que los transforma en instrucciones, advertencias o visualizaciones con fines de evaluación. Como este sistema Nexeed Production Performance Manager ha demostrado ser una solución ideal para el primer banco de ensayos, HBM tiene intención de ampliarlo en los próximos meses a un total de 20 equipos, cada uno de ellos con una problemática distinta. La colaboración entre HBM y Bosch ha puesto a disposición de los clientes de HBM una tecnología innovadora de ensayos y medición, con opciones de análisis y evaluación, con la garantía adicional de unas prestaciones máximas en entornos complejos de hardware y software, en los plazos de tiempo más cortos posible.
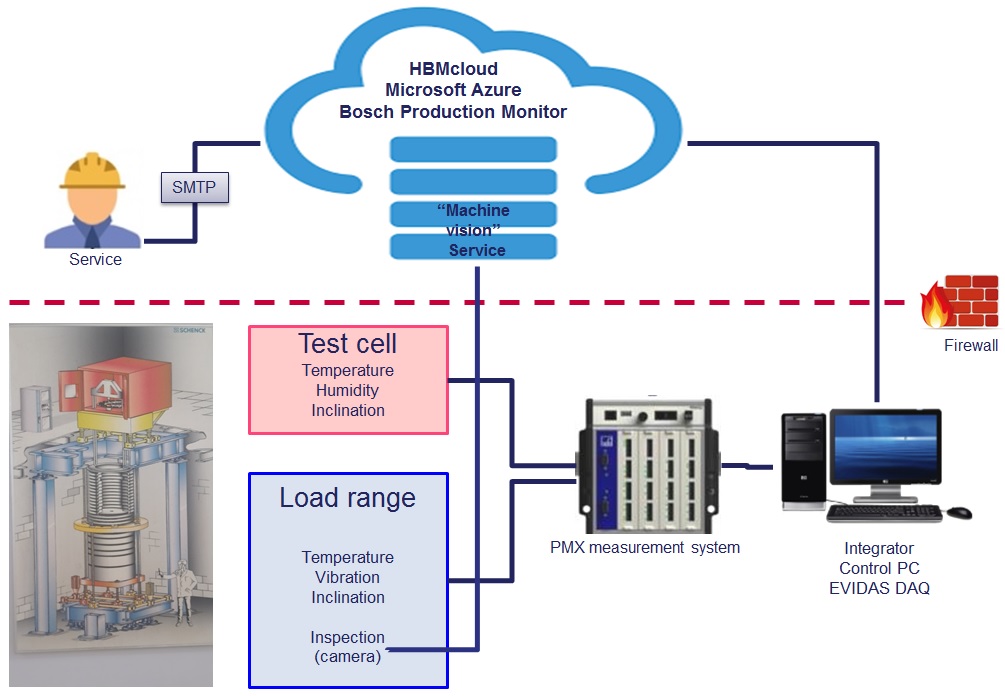
Plug-and-Run en tres fases
En una primera fase, se analizó el funcionamiento del sistema y se determinaron los puntos relevantes de monitorización de la maquinaria. A continuación se seleccionaron los sensores y la tecnología de medición más adecuados. La parte superior del sistema de calibración es la cámara de ensayo. En ella se colocan los sensores que se desea calibrar (transductores de fuerza y células de carga), junto con sensores de temperatura, humedad e inclinación. En la parte inferior se encuentran grandes pesos que se mueven mediante motores eléctricos para generar las cargas de calibración. Estos procesos mecánicos se monitorizan, a su vez, utilizando sensores de temperatura, vibración e inclinación.
En una segunda fase, se seleccionó la tecnología de medición más idónea. PMX es un sistema de medida multicanal capaz de adquirir datos y de procesarlos en tiempo real. Ofrece amplias funciones de diagnóstico y se puede parametrizar a través de un servidor web compatible con una red. Todos los datos medidos se registran y evalúan con una frecuencia de muestreo de 19,2 kHz. Los datos de medida y de diagnóstico se transmiten a un hub de IoT utilizando una interfaz Ethernet estándar (TCP/IP). Este hub consiste en un PC equipado con un software de adquisición de datos adecuado.
En la tercera fase, se buscó una nube y un software de evaluación adecuados. La mejor opción era, por supuesto, utilizar la nube de HBM ya existente. La gran ventaja de la tecnología de medida basada en la nube radica en que elimina la necesidad de mover los datos de un punto de almacenamiento a otro. Su valor añadido resulta perceptible inmediatamente, en muchos casos incluso de forma automática, gracias al uso de inteligencia artificial. La nube de HBM permite acceder a los datos en todo el mundo —con autorización— y mejora el flujo de información y el trabajo de los equipos internacionales. Elegir el socio en la nube “correcto” era un pilar vital de esta estrategia. HBM eligió a Microsoft Azure. Este proveedor resultó especialmente convincente porque dispone de docenas de centros de datos repartidos por todo el mundo, en donde los datos se almacenan de manera conforme con los requisitos legales asociados a la ubicación de cada empresa.
Conexión rápida y flexible de máquinas a la industria 4.0
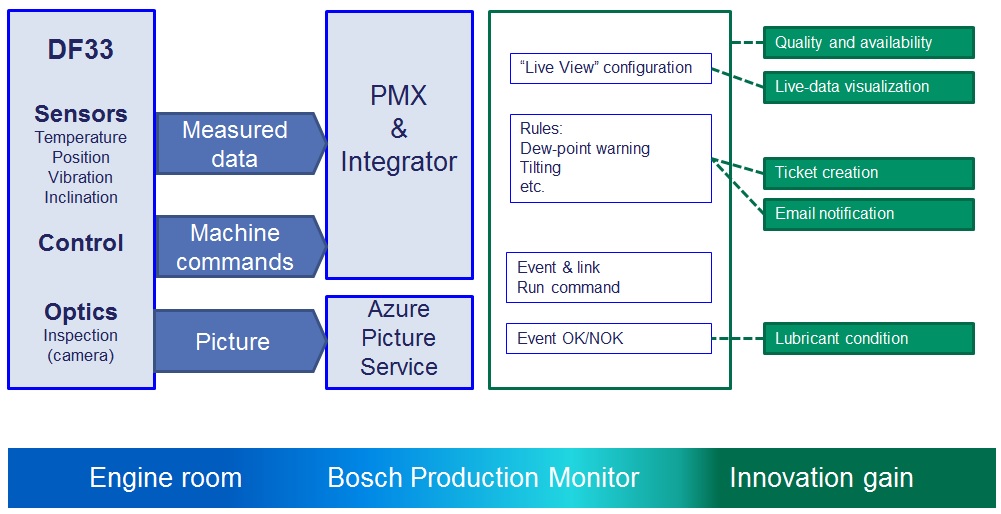
Ventajas
La conexión en red de máquinas nuevas o ya existentes de forma económica permite optimizar los procesos de producción y la calidad del producto. La pasarela PMX al IoT y el software de adquisición de datos facilitan la conexión a entornos Industria 4.0, sin interferir con la lógica de automatización. Una combinación adecuada de equipos y software de control para aplicaciones de TI se encarga de recoger datos de sensores y procesos, los transmite (a MES, aplicaciones en la nube o sistemas de monitorización local del estado de máquinas) y hace posible el análisis de los datos de proceso.
- Mayor productividad y eficiencia.
- Plug-and-Run en tres fases
- Modularidad adaptada a los requisitos individuales.
- Equipos de medida (PMX) y software escalables y robustos.
- Arquitectura de software abierta, orientada al futuro, y uso de la nube de HBM.